What is a industrial textile shredder?
Table of Content
- Industrial Textile Shredders
- Types of Industrial Textile Shredders
- Key Features of Industrial Textile Shredders
- How Industrial Textile Shredder Works
- Detailed Process
- Applications
- Factors Influencing Industrial Textile Shredders Price
- FAQs about Industrial Textile Shredders
- Conclusion
Industrial Textile Shredders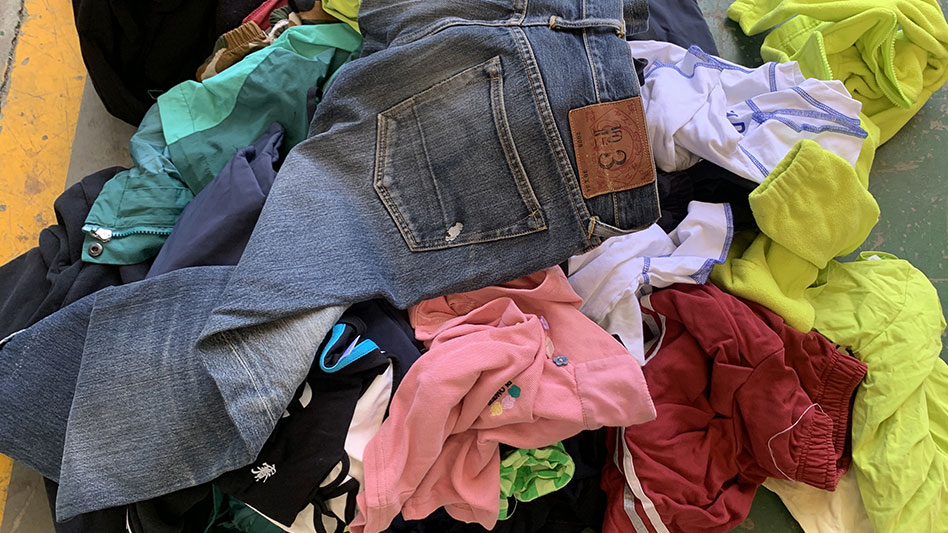
A industrial textile shredder is a machine designed to reduce fabric materials into smaller pieces or fibers. These machines are commonly used in the recycling and waste management industry to process old clothing, fabric scraps, and other textile materials.
Types of Industrial Textile Shredders:
- Single-Shaft Shredders: These shredders have one rotating shaft with cutting blades and are suitable for processing smaller volumes of textiles.
- Dual-Shaft Shredders: Featuring two rotating shafts, these machines can handle larger volumes and tougher materials, making them ideal for industrial applications.
Key Features of Industrial Textile Shredders:
- 용량: Depending on the volume of textiles to be processed, the capacity of the shredder is an important factor.
- Cutting Mechanism: Different shredders have varying cutting mechanisms, which affect the size and uniformity of the shredded pieces.
- Durability and Maintenance: Industrial shredders are robust and easy to maintain to ensure long-term, efficient operation.
How Industrial Textile Shredder Works: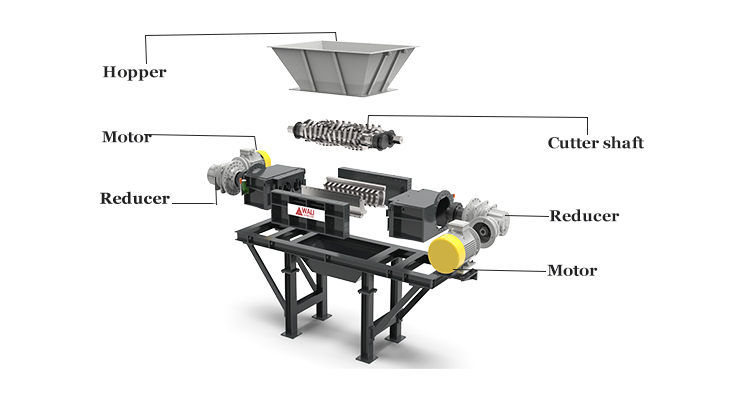
-
Feeding:
- Input Hopper: Textile materials are fed into the shredder via an input hopper. This can be done manually or through automated systems like conveyors.
- Feeding Mechanisms: For continuous and efficient feeding, some industrial textile shredders use hydraulic rams or conveyors to push materials into the cutting chamber.
-
Cutting and Shredding:
- Cutting Blades: The core of the shredder consists of rotating cutting blades mounted on shafts. In dual-shaft shredders, two shafts rotate in opposite directions.
- Shear Force: As the blades rotate, they create a shear force that cuts and tears the textile materials into smaller pieces. The design and arrangement of the blades determine the size and consistency of the shredded material.
- Screens: Some shredders use screens with specific hole sizes to control the final size of the shredded pieces. Material that is too large is recirculated back into the cutting chamber for further shredding.
-
Discharge:
- Conveyor Belts: Shredded materials are discharged onto conveyor belts for further processing, storage, or transportation.
- Output Hoppers: In some setups, shredded material falls directly into output hoppers or bins for collection.
Detailed Process: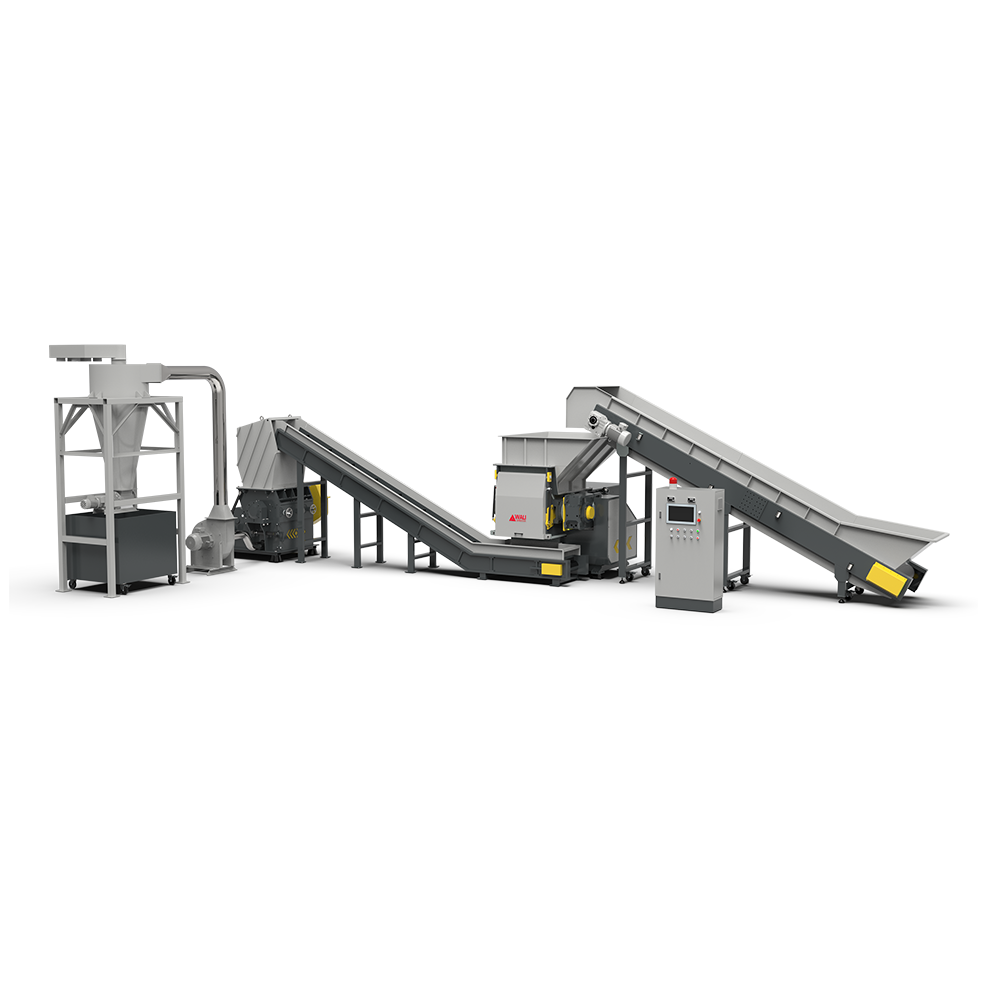
-
Material Intake:
- Loading: Large bales or rolls of textiles are loaded into the shredder. Depending on the machine, this might require pre-processing to cut the materials into smaller sections.
- Automated Feeders: For high-volume operations, automated feeders ensure continuous and consistent material flow into the shredder.
-
Primary Shredding:
- Initial Reduction: The textile material is grabbed by the rotating shafts. The intermeshing of the blades on the shafts applies both a tearing and slicing action.
- High Torque, Low Speed: Industrial shredders often operate at low speeds but with high torque to handle dense and tough textile materials, preventing jams and ensuring effective shredding.
-
Secondary Processing:
- Re-shredding: If the material needs to be further reduced, it can pass through additional shredding stages or be processed by a granulator.
- Separation: In some systems, additional separation equipment may be used to remove contaminants or separate different types of materials (e.g., separating metal fasteners from fabric).
-
Material Output:
- Transport Systems: Conveyor belts transport the shredded material to storage areas or directly to the next stage of processing.
- Baling or Bagging: Shredded materials can be compacted into bales or bagged for easier handling and transport.
Applications:
- Clothing Recycling: Old or unwanted clothing can be shredded and recycled into new fabrics or other products.
- Manufacturing Waste: Fabric scraps from garment manufacturing can be shredded and reused, reducing waste.
- Non-Woven Fabrics: Shredded textiles can be used to produce non-woven fabrics for various applications, such as automotive interiors or geotextiles.
Factors Influencing Tire Shredder Price
1.Tire Shredder Configuration
- Blade Type and Material: Different shredders use various blade configurations and materials (e.g., 강철) for durability and efficiency.
- Motor Power: Ranges from 50 HP to over 500 HP depending on the shredder’s size and capacity.
- Brand and Manufacturer: Reputable brands with a history of reliability and performance will significantly impact its cost.
- Customization: Machines tailored for specific applications or with special configurations may be more expensive.
2. Additional Costs
- Shipping and Transportation: Depending on the location, transporting a large tire shredder can add several thousand dollars to the total cost.
- Installation and Setup: Professional installation and setup will be an expense.
- Maintenance and Spare Parts: Ongoing maintenance and the cost of replacement parts should be factored into the overall budget.
FAQs about Industrial Textile Shredders
Q:What are the benefits of Industrial Textile Shredders ?
A: Facilitating resource recovery, reducing costs in transportation and storage.
Q: What is the price of a Industrial Textile Shredders ?
A: The price of a Industrial Textile Shredder can vary significantly depending on its size, capacity, discharge size, motor brands and so on.
Conclusion
By systematically reducing textile waste into smaller, manageable pieces, industrial textile shredders play a crucial role in recycling and waste management, helping industries manage waste more efficiently and sustainably.When choosing a industrial textile shredders, it’s essential to consider factors such as the type of materials, the volume of material, discharge size , installation space and budget.