What is a aluminum can shredder?
Table of Content
- Aluminum Can Shredders
- Key Features of Three Types of Aluminum Can Shredders
- Industrial Aluminum Can Shredders
- How Industrial Industrial Aluminum Can Shredders Operate
- Factors Influencing Aluminum Can Shredders Price
- FAQs about Aluminum Can Shredders
- Conclusion
Aluminum Can Shredders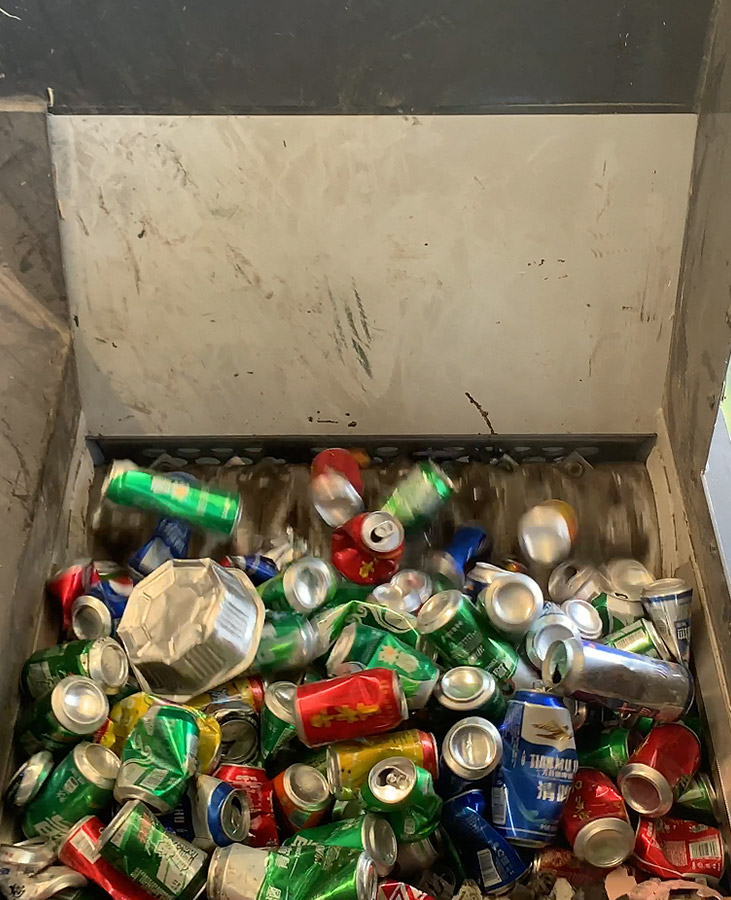
An aluminum can shredder is a machine designed to reduce aluminum cans into smaller pieces for recycling purposes. These shredders can handle large volumes of cans, making the recycling process more efficient. There are different types of aluminum can shredders, ranging from small, manual models to large, industrial-scale machines.
Key Features of Three Types of Aluminum Can Shredder:
Feature | Industrial | Small | Manual |
Capacity | High thousands of cans per hour | ModerateSuitable for small batches | Low, one can at a time |
Operation | Electric,automated feeding | Electric or manual | Manual Hand operated |
Size | Large,Requires significant space | Compactfits in small space | Very compact, portable |
Durability | Extremely durable,Built for Continuous use | Durable but lessso than industrial | Durable for regularhome use |
Safety Features | Advanced safety mechanisms | Basic safety features | Basic safety features |
Cost | High | Moderate | Low |
Energy Efficiency | Designed for energy efficiency | Generally efficient | No energy required |
Maintenance | Requires regular maintenance | Minimal maintenance | Minimal maintenance |
Portability | Fixed installation | Portable | Highly portable |
Use Case | Recycling centers, metal processing facilities | Home use, small businesses | Home use, small-scale recycling |
This table highlights the key differences and features of industrial, small, and manual aluminum can shredders, which will help us to determine the best option based on specific needs. Next, we will focus on industrial aluminum can shredders.
Industrial Aluminum Can Shredders:
Industrial aluminum can shredders are heavy-duty machines designed to handle large volumes of cans efficiently. They are used in recycling centers, metal processing facilities, and other industrial settings. These shredders are robust, durable, and capable of continuous operation to manage high throughput.
How Industrial Industrial aluminum can shredders Operate:
-
Feeding
- Input Hopper: Aluminum cans are loaded into a large hopper or conveyor belt. The hopper can handle large quantities, allowing continuous feeding.
- Automated Feeding System: In many industrial setups, a conveyor belt system automatically feeds cans into the shredder, ensuring a steady and controlled flow.
-
Shredding
- Cutting Mechanism: The cans are drawn into the shredder where they encounter rotating blades or hammers made of hardened steel. These cutting mechanisms are designed to shear, tear, and crush the aluminum.
- Primary Shredding: The initial set of blades or hammers begins to cut the cans into smaller, more manageable pieces.
- Secondary Shredding: Some industrial shredders have multiple stages of shredding to ensure the material is finely processed.
-
Separation and Sorting
- Magnetic Separation: After shredding, the pieces may pass through magnetic separators to remove any ferrous (iron-containing) contaminants, ensuring only aluminum remains.
- Air Classification: Air classifiers or blowers can be used to separate lighter aluminum fragments from heavier contaminants or other materials.
-
Output and Collection
- Output Conveyor: Shredded aluminum is typically moved away from the shredding area via conveyor belts.
- Collection Bins: The shredded material is collected in bins or containers for further processing, such as baling or smelting.
-
Safety and Efficiency Features
- Safety Guards: Industrial shredders are equipped with various safety features like emergency stop buttons and safety guards to protect operators.
- Overload Protection: Many machines have sensors to detect overload conditions and automatically shut down or reduce feed rates to prevent damage.
- Energy Efficiency: Modern industrial shredders are designed to maximize energy efficiency, reducing operational costs and environmental impact.
-
Control Systems
- Automated Control Panels: Operators use control panels to manage and monitor the shredding process, adjusting speeds, feed rates, and other parameters as needed.
- Monitoring Systems: Advanced systems can include real-time monitoring and diagnostics to ensure optimal performance and quick troubleshooting.
Factors Influencing Aluminum Can Shredders Price:
-
Aluminum Can Shredders Configuration
- Blade Type and Material: Different shredders use various blade configurations and materials (e.g., steel) for durability and efficiency.
- Motor Power: Ranges from 50 HP to over 500 HP depending on the shredder’s size and capacity.
- Brand and Manufacturer: Reputable brands with a history of reliability and performance will significantly impact its cost.
- Customization: Machines tailored for specific applications or with special configurations may be more expensive.
-
Additional Costs
- Shipping and Transportation: Depending on the location, transporting a large tire shredder can add several thousand dollars to the total cost.
- Installation and Setup: Professional installation and setup will be an expense.
- Maintenance and Spare Parts: Ongoing maintenance and the cost of replacement parts should be factored into the overall budget.
FAQs about Aluminum Can Shredders
Q:What are the benefits of Aluminum Can Shredders ?
A: Enables the extraction of valuable metals like aluminum; reducing costs in transportation and storage.
Q: What is the price of a Aluminum Can Shredder ?
A: The price of a aluminum can shredder can vary significantly depending on its size, capacity, discharge size, motor brands and so on.
Conclusion:
Aluminum can shredders are essential for waste recycling operations, helping to reduce waste and recycle materials efficiently.When choosing a aluminum can shredder, it’s essential to consider factors such as the type of materials, the volume of material, discharge size , installation space and budget.